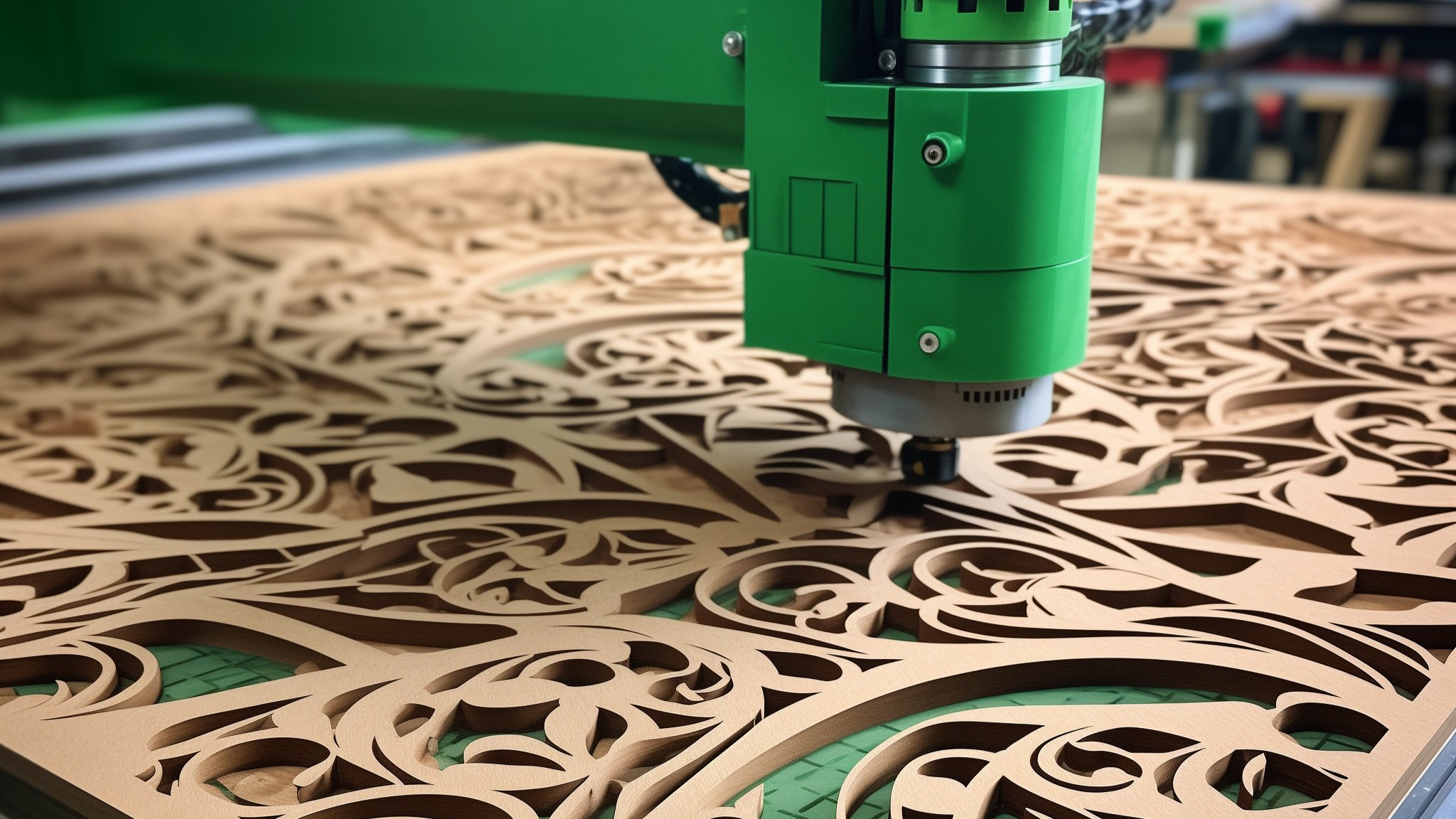
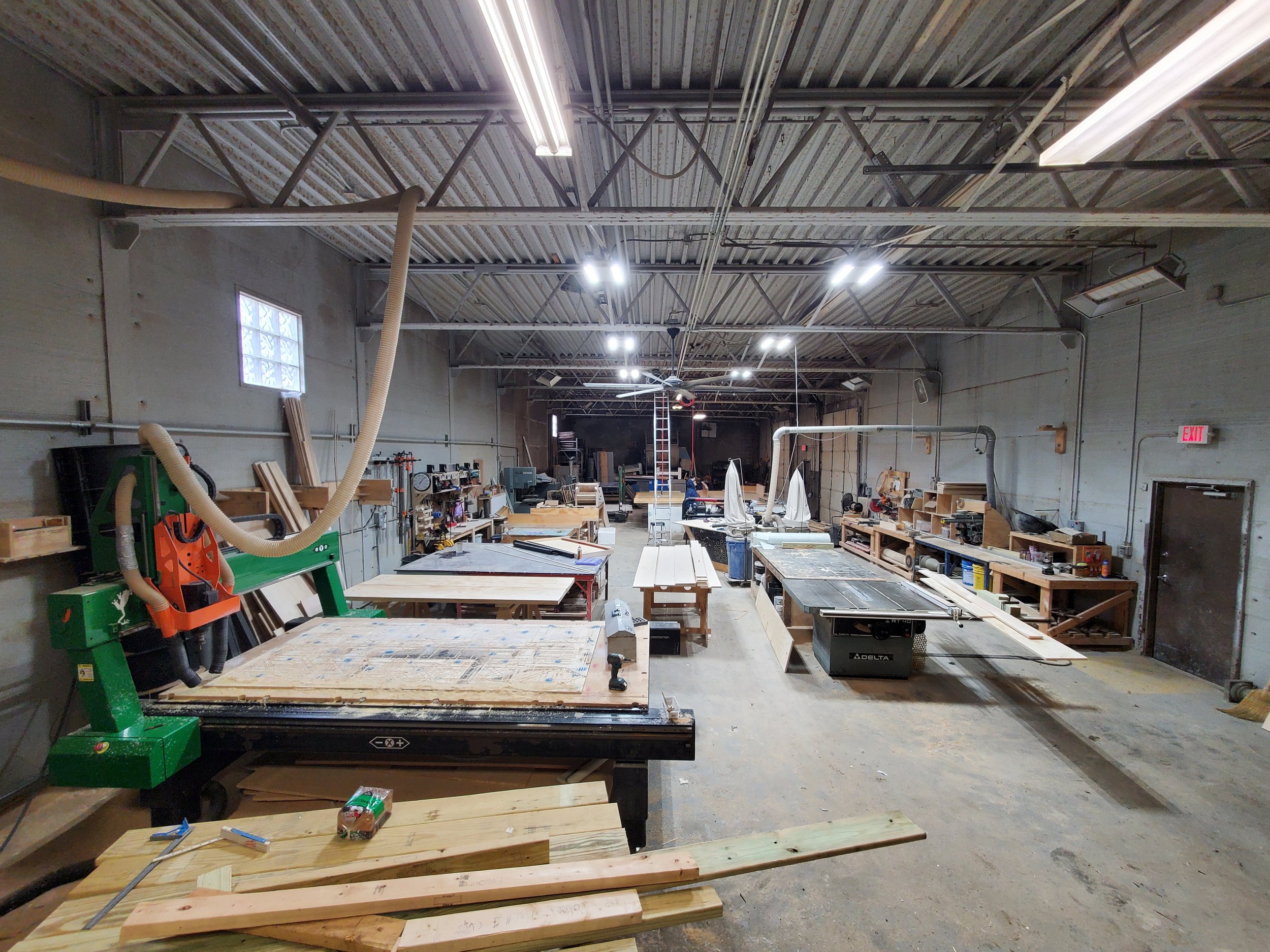
Step 1 - Mold Making Wood Shop
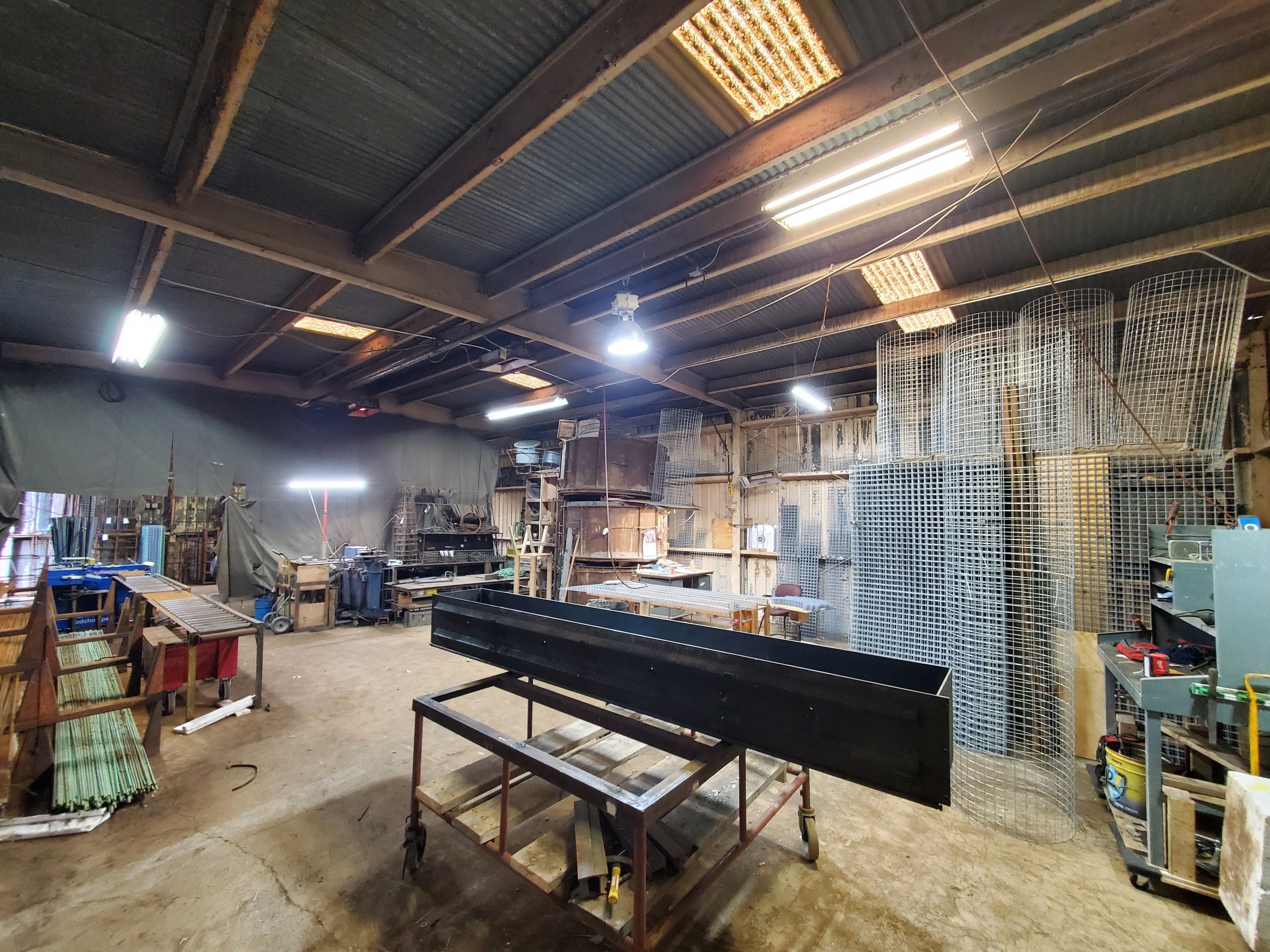
Step 2 - Metal Cage Shop
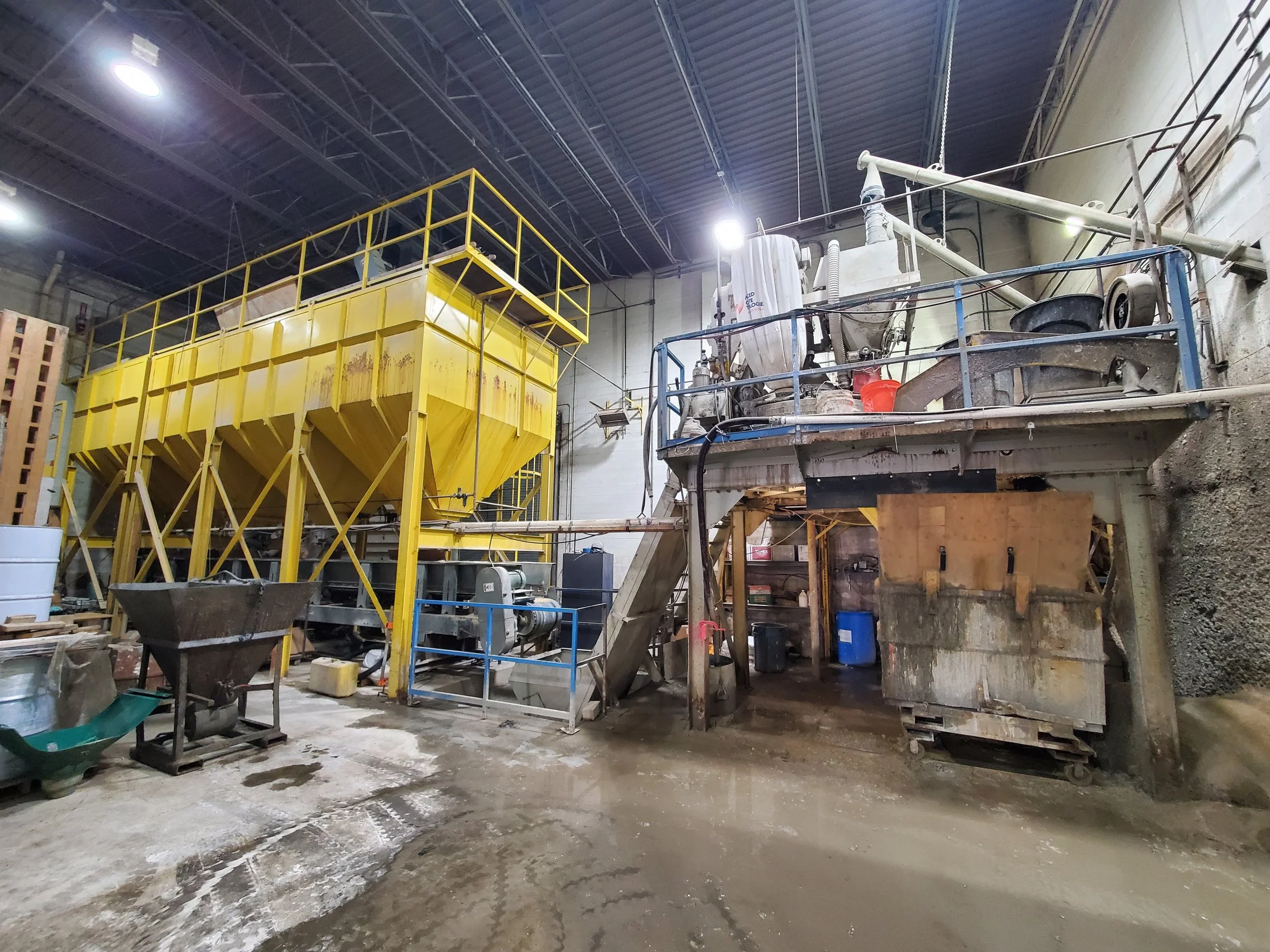
Step 3 - Mixer
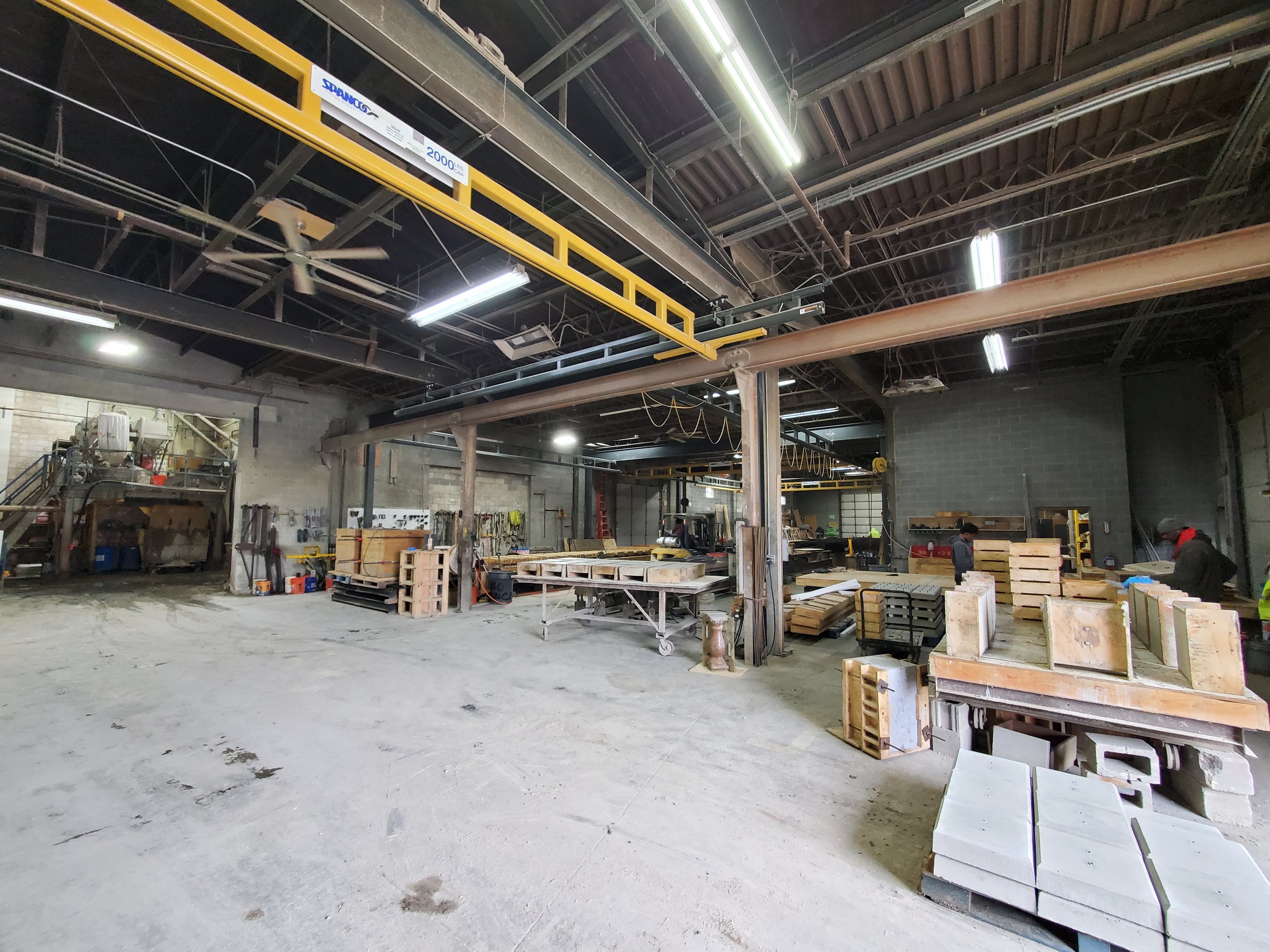
Step 4 - Pouring & Casting
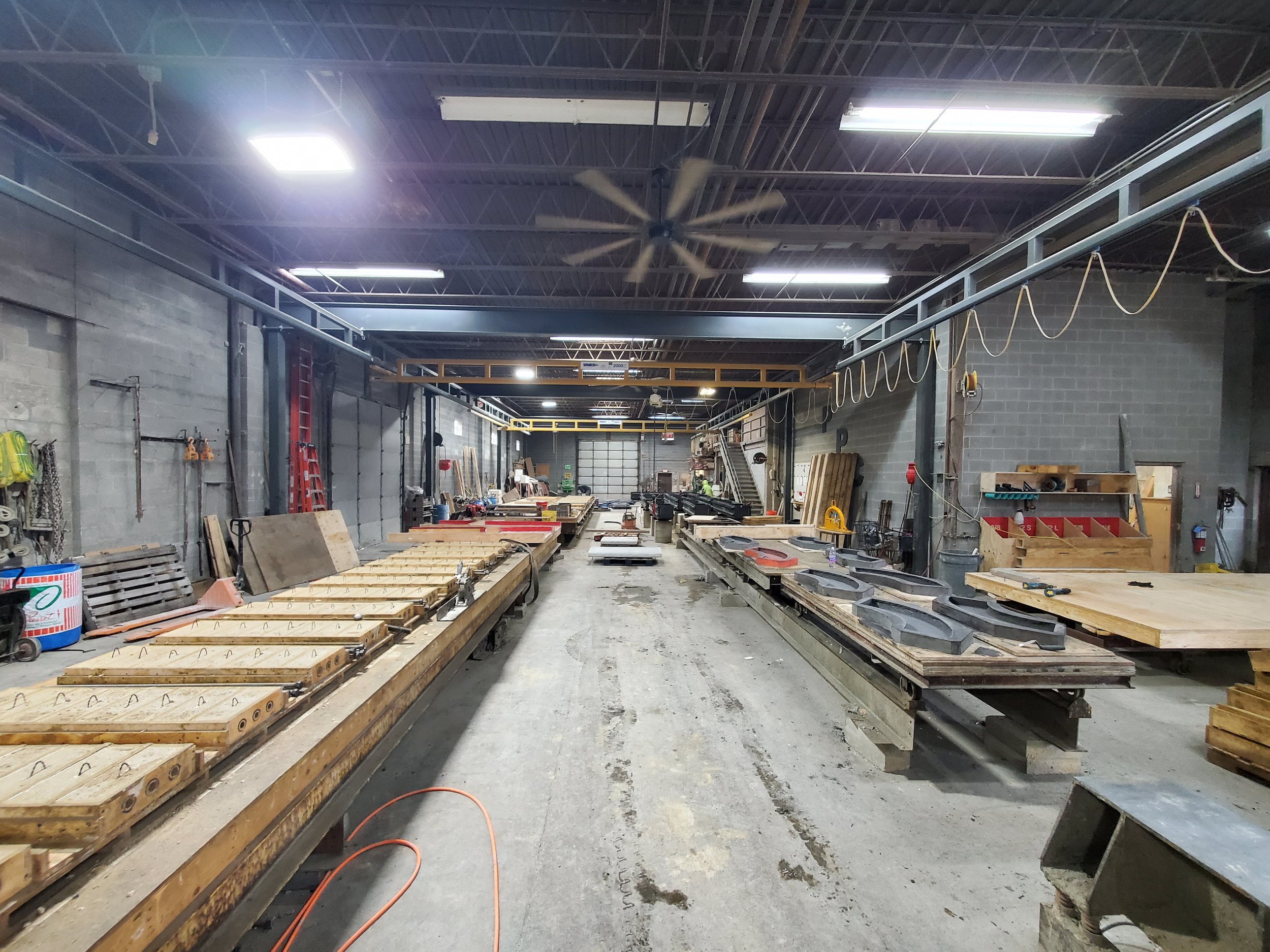
Step 4 - Pouring & Casting
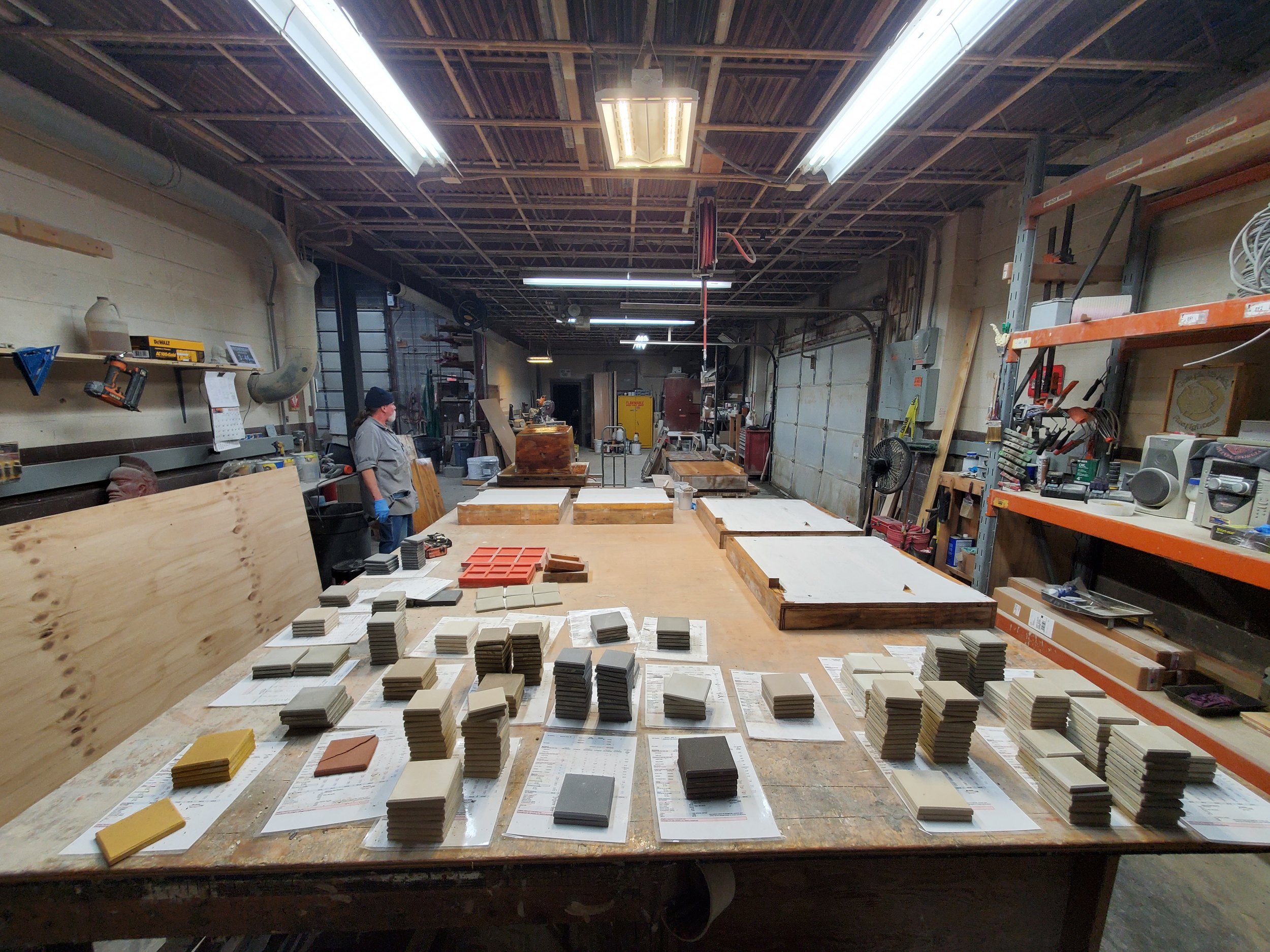
Step 7 - Finishing
The precast concrete process offers advantages such as consistency, cost-effectiveness, versatility, durability and reduced construction time compared to cast in place and natural stone. Strict quality control measures are implemented throughout the manufacturing process to ensure that the precast concrete meets the required standards and specifications. Here is a description of our precast concrete manufacturing process:
Part Design & Mold
The process begins with the design of the precast concrete product. This can be based on architectural plans or specific product requirements.
Once the design is finalized, molds are created to shape the precast concrete. These molds are typically made from wood, rubber, steel or fiberglass that can withstand the casting process.
Reinforcement (if necessary):
Depending on the application and structural requirements, reinforcement materials such as rebar(epoxy coated or bare), galvanized wire mesh, and or fibers may be added to the concrete mix to enhance strength, durability and longevity.
Mixing:
The prepared materials are mixed in a concrete mixer to ensure a homogeneous blend. The mixing process is critical for achieving the desired consistency and strength of the precast concrete.
Precast concrete is made from a mixture of aggregates, cement, and water. Special additives may be included to enhance the properties of the final product. These include densifiers, plasticizers and water repellents.
The aggregates can include crushed stone, sand, and other materials that contribute to the desired appearance and strength of the precast stone.
Casting:
The mixed concrete is poured into the prepared molds. Vibrators are used to eliminate air bubbles and ensure a smooth architectural and dense surface finish.
The molds are carefully filled to avoid any voids or imperfections in the precast concrete.
Curing:
After casting, the precast stone undergoes a curing process to allow the concrete to achieve its optimal strength. This is done in a controlled environment with regulated temperature and humidity.
Demolding:
Once the curing is complete, the precast stone is removed from the molds. The demolding process requires care to prevent any damage to the finished product.
Finishing:
After demolding, the precast stone undergoes additional finishing processes, such as sanding, polishing, staining, or acid etching to achieve the desired aesthetic qualities.
Transportation and Installation:
The finished precast stone products are transported to the construction site and installed according to the project's requirements. We can handle an array of shipping methods that allow contractors to easily handle and set any kind of project.